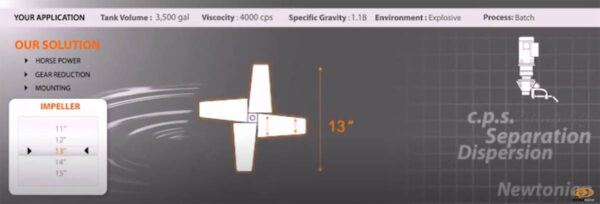
Mixing 101: Optimal Mixer Design
4 FACTORS FOR OPTIMAL CONFIGURATION Getting the right mixer for the job involves so much more than simply purchasing a standard unit off-the-shelf. There is an art to configuring a mixer that will optimize the results of an application. Selecting a mixer based solely on horsepower or RPM requirements can produce less than optimal results, and even damage your product through excessive shear. As we discussed in an earlier post, we first need to understand the 4 Factors for Configuring a Mixer, which are: Tank Type & Volume Fluid Viscosity Specific Gravity Environment & Process Once a Dynamix Sales Engineer understands these factors in relation to your application needs, we are ready to configure a mixer that will both maximize your investment